Plastic extrusion for high-volume custom plastic parts
Plastic extrusion for high-volume custom plastic parts
Blog Article
Key Advantages and Considerations of Carrying Out Plastic Extrusion in Your Projects
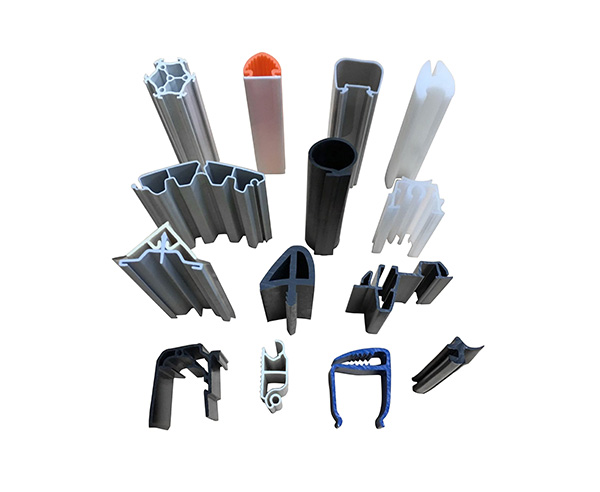
Recognizing the Fundamentals of Plastic Extrusion
Plastic extrusion, a staple in the manufacturing sector, is a procedure that includes melting raw plastic material and improving it into a continuous account. This profile, once cooled down, can be reduced into desired sizes or coiled for later usage. The appeal of plastic extrusion lies in its adaptability. A broad range of items, from piping to home window frames, can be generated. The procedure requires an extruder, an intricate machine with a warmed barrel, a turning screw, and a die at the end. The plastic material, in the form of pellets, is fed right into the extruder, where it's thawed and required through the die, taking its form. The option of plastic and the style of the die identify the product's features.
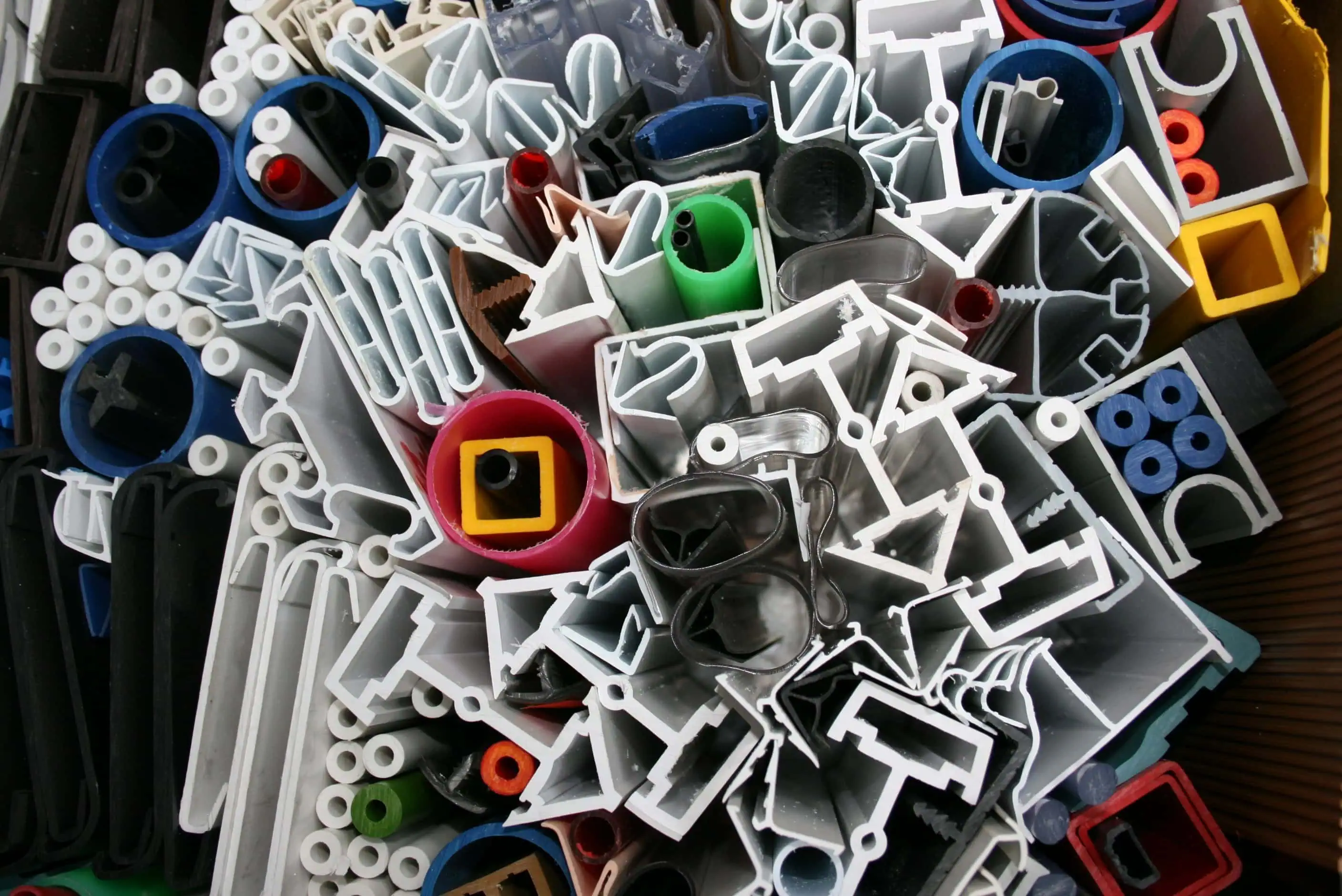
The Economic Benefit of Plastic Extrusion
The economic benefit of plastic extrusion lies mostly in 2 locations: affordable material manufacturing and valuable manufacturing speeds. With plastic extrusion, organizations can create high volumes of product at a lower expense compared to other techniques. Furthermore, the process boasts a remarkable manufacturing speed, considerably minimizing time and more enhancing its financial feasibility.
Cost-Effective Material Production
A significant advantage of plastic extrusion is its remarkable cost-effectiveness. In addition, the extrusion process permits for a high degree of accuracy in shaping the plastic, minimizing the need for pricey post-production modifications or adjustments. All these variables make plastic extrusion an extremely affordable choice for several projects, using an attractive balance in between cost and efficiency.
Beneficial Production Speeds
While keeping the cost-effectiveness of the products, an additional notable benefit of plastic extrusion exists in its fast production speeds. This combination of cost-effectiveness, rate, and top quality underscores the considerable economic benefit of applying plastic extrusion in different jobs.
Flexibility and Customization: The Strengths of Plastic Extrusion
Among the noticeable staminas of plastic extrusion hinges on its flexibility and customization possibility. These high qualities unlock to endless style possibilities, offering makers the ability to customize items to particular demands. This increased level of modification not only boosts product functionality but likewise considerably boosts product originality.
Limitless Design Possibilities
Plastic extrusion shines in its capacity to use almost infinite design opportunities. This method supplies liberty to produce elaborate accounts and complicated forms, a feat difficult to attain with other construction strategies. Owing to the fluid nature of molten plastic, the procedure is flexible enough to generate a varied variety of forms, dimensions, and dimensions. The plastic can be controlled to match one-of-a-kind specifications, enabling for the manufacturing of tailored geometries and meeting particular customer demands. Plastic extrusion can deal with a selection of plastic kinds, expanding its application extent. This versatile technique, for that reason, offers a large range of markets from construction to vehicle, product packaging to electronic devices, and beyond. With plastic extrusion, the design opportunities are virtually endless.
Improving Product Originality
The convenience of plastic extrusion can considerably improve item individuality. This process permits designers to try out different forms, sizes, and shades, providing the liberty to produce distinct products that stand out on the like it market. It is this customization that offers a distinctive identity to each item, differentiating it from its competitors.
In addition to its visual advantages, the customizability of plastic extrusion additionally uses practical advantages. Hence, plastic extrusion not only improves item uniqueness yet also its utility and marketability.
Layout Limitations in Plastic Extrusion: What You Required to Know
How can make limitations possibly affect the process of plastic extrusion? While plastic extrusion is functional, design limitations can cut its benefits. Certain complicated layouts might not be possible because of the constraints of the extrusion process, potentially limiting the imp source production of intricate accounts. The procedure is much less suitable for multi-chambered or hollow frameworks. Additionally, the extrusion process might not constantly provide the preferred surface area coating, particularly for those calling for high gloss or optical clarity. Product selection can additionally pose difficulties, as not all polymers are suitable for extrusion. High-temperature immune plastics, for instance, may offer difficulties. Understanding these restraints is vital for effective implementation of plastic extrusion in your jobs. plastic extrusion.
Assessing the Ecological Influence of Plastic Extrusion
While understanding layout restrictions is a substantial facet of plastic extrusion, it is just read what he said as crucial to consider its ecological implications. The process of plastic extrusion includes melting plastic products, possibly launching hazardous gases right into the setting. Making use of recycled plastic materials in the extrusion process can minimize ecological effect.

Instance Research Study: Successful Projects Utilizing Plastic Extrusion
Success stories in the field of plastic extrusion are plentiful, demonstrating both the adaptability and performance of this manufacturing process. plastic extrusion. One more successful situation is the manufacturing of plastic film for product packaging and farming. These circumstances show plastic extrusion's critical function in numerous industries, testifying to its flexibility, cost-effectiveness, and reliable output.
Conclusion
In final thought, plastic extrusion provides a effective and cost-effective approach for generating complicated shapes with marginal waste. Including plastic extrusion into projects can lead to successful results, as shown by many instance researches.
Plastic extrusion, a staple in the production industry, is a process that involves melting raw plastic material and reshaping it into a constant account. Plastic extrusion can take care of a variety of plastic types, broadening its application extent.How can create constraints possibly affect the process of plastic extrusion? The process of plastic extrusion includes melting plastic products, possibly releasing harmful gases into the atmosphere. Using recycled plastic materials in the extrusion procedure can decrease ecological impact.
Report this page